Construction process of chemical resistant epoxy paint KERAGUARD VL100
KERAGUARD VL100 is a novolac two-component, 100% solid, chemical resistant epoxy coating system used in horizontal construction. KERAGUARD VL100 has good flow ability and high efficiency for both steel and concrete.
Uses of chemical resistant epoxy paint KERAGUARD VL100
- Chemical production factory.
- Chemical and water storage tanks
- Chemical storage area
- Food and beverage production factories
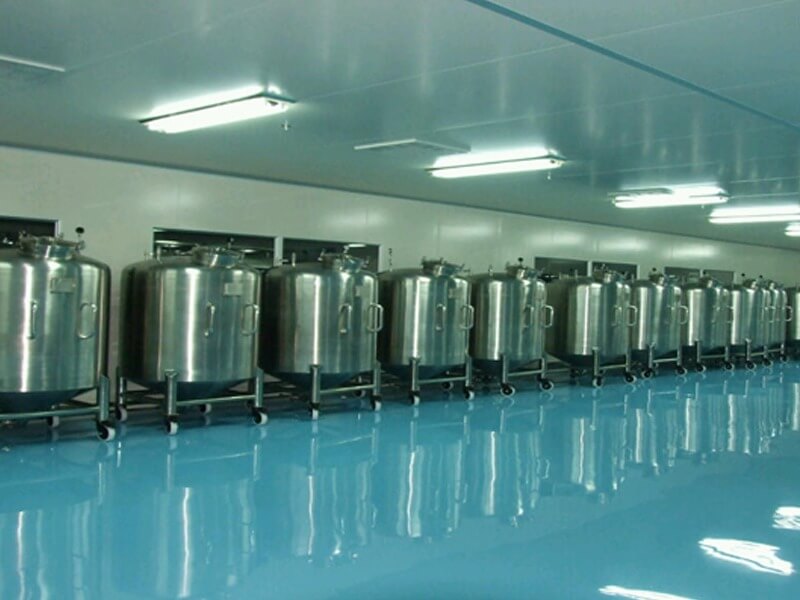
Advantages of chemical resistant epoxy paint KERAGUARD VL100
-
Less odor
- Good chemical resistance
- Good protection and abrasion resistance
- Increase abrasion resistance when using with silica sand
- Many color options.
Construction steps and notes when applying chemical resistant paint KERAGUARD VL100
Construction process of KERAGUARD VL100 includes the following steps:
Step 1: Mix part A into part B
Tool to use: Specialized mixer at about 600 rpm with mixing paddle.
Component A is pre-mixed for 2-3 minutes until the material is homogeneous.
Pour part B onto part A, mix for 2-3 minutes until homogeneous.
Note: Do not mix for too long to avoid air bubbles during material mixing.
Once this material is mixed it cannot be resealed for later use.
Step 2: Preparation of concrete floor surface
Use a concrete floor grinder to create roughness and then use a vacuum cleaner to clean the floor surface.
Step 3: Apply the primer
Primer product used before applying KERASEAL VL100 is KERASEAL PS60. This is a solvent-based epoxy primer, which increases the adhesion between the concrete and the next epoxy coatings. The constructors need to perform this step before applying the topcoat.
With porous concrete floor, it can apply 1 more primer to achieve the required surface. For steel surfaces, a corrosion resistant primer is recommended.
The primer is rolled as thin as possible. Consumption is from 0.1 - 0.2 kg / 1m2. After at least 1 day, the primer dries, the constructor can light traffic to patch the surface.
Step 4: Surface patching
The floor patching product used is KERACRETE NS50. This is a non-sagging 2 component epoxy system. It is an ideal product to be used in a variety of mortars, fillings, and repair cracked concrete surfaces. Surface drying time is 3 hours 30 minutes. The average consumption is 1.5kg / m2 can be applied with a thickness of 1 mm2.
Step 5: Apply the basecoat
In order to do this step, the constructor can use a short hair roller. If using airless spray, use a single line piston pump with a 45:1 ratio may be used, using a 0.025inch tungsten nozzle tip.
Note: Do not add solvents to the construction materials because they will slow down the hardening process, significantly affect the maintenance process, especially in the case of soaking in water.
Step 6: Apply the topcoat
After applying the basecoat for at least 1 day, the constructor can apply the topcoat. After about 5 - 10 days the floor coating is completely hardened, the factory can use.
To get direct advice from APT Vietnam about industrial floor paint, investors and contractors please contact phone number 0904 339 299!