KERASEAL ADO40 – Self-leveling epoxy paint of APT Vietnam
KERASEAL ADO40 is a self-leveling, solvent-free and phenol epoxy coating system. This product is often used in many electronic component factories, food and beverage factories. So what are the advantages of KERASEAL ADO40? What should be noted during construction?
The outstanding advantage of self-leveling epoxy paint KERASEAL ADO40
- Antibacterial and easy to clean: Unlike the tiles that are easy to dust in the circuit, KERASEAL ADO40 gives the factory a smooth and easy to clean concrete protection layer. They help the factory to remove grease, dirt, general chemicals. Absolute antibacterial ability and super smooth surface help KERASEAL ADO40 score when constructing in clean rooms, hospitals, pharmaceutical factories.
- High wear and abrasion resistance: This is the most outstanding advantage of these self-leveling paint lines. They are known as self-leveling paints with high abrasion of 0.65 mg / cm2. Impact resistance is 68kg.cm. The factory can completely move on the floor of large trolleys with no need to worry.
- Self-leveling ability: Completely covers the holes, creating a flat surface because of self-leveling mechanism of the paint.
- Saving repair costs: KERASEAL ADO40 is a product that has been constructed in many projects and is highly appreciated. So the factory is completely assured about the project quality. Floors are used for a long time without the problem of peeling or blistering. After about 5 - 6 years, the factory only needs to repaint the topcoat to be able to continue to use as new.
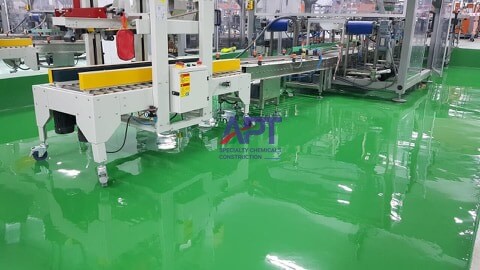
Notes on the application of KERASEAL ADO40
Application process of KERASEAL ADO40 includes 6 steps:
Step 1: Mix part A and B
The constructor should use a specialized mixer at a speed of about 600 rpm with a suitable mixing paddle. First, mix part A for 2-3 minutes until homogeneous material. Add part B to part A and mix a further 2 - 3 minutes until homogeneous. Do not mix for too long to avoid air bubbles during material mixing.
Note: Once this material is mixed it cannot be resealed for later use.
Step 2: Surface preparation
- Concrete floor conditions to use KERASEAL ADO40 is smooth surface and humidity <6%. The constructor needs to measure the humidity for the concrete floor. Especially, avoid construction when it rains, the weather is humid, with high humidity.
- Then, the builder needs to use the rubbing machine to smooth the concrete floor. Use a vacuum cleaner to clean any remaining dirt on the floor.
Step 3: Applying the primer
Primer product used before applying KERASEAL ADO40 is KERASEAL PS60. This is a solvent-based epoxy primer. They will increase the adhesion between the concrete and continuous coatings. Therefore, this step must be performed by the builder before applying the basecoat. The primer is rolled as thin as possible. Consumption is from 0.1 - 0.2 kg / 1m2. After at least 1 day, the primer dries, the constructor can light traffic to patch the surface.
Step 4: Patching surface
The surface patching product used is KERACRETE NS50. This is a non-sagging 2-component epoxy system. It is an ideal product to be used in a variety of mortar, fillings, and repair cracked concrete surfaces. Surface drying time is 3 hours 30 minutes. The average consumption is 1.5kg / m2 applied with a thickness of 1 mm2.
Step 5: Applying the basecoat
For glossy and self-leveling surfaces
Spread the pre-mixed materials in the correct ratio on the prepared concrete surface, using the dressing table to spread the material evenly with the required thickness. Because the surface is self-leveling, use a spiked roller to break air bubbles.
For anti-slip surfaces
With an anti-slip surface, the constructor needs to use silica sand layer after finishing by spiked roller. This helps the floor to increase hardness. In addition, they also help the factory to save construction materials.
When the surface dries, wipe off any excess sand. Surface should be sanded to achieve high aesthetics and reduce material consumption density.
Step 6: Apply the topcoat
The maximum time for next coating is 72 hours. Minimum next coating time is 12 hours. Therefore, after at least 1 day, the constructor can apply the topcoat.
Constructors need to use a serrated trowel to spread paint evenly. Then, use a spiked roller to break air bubbles on the factory floor. After 1 day, customer can light traffic. After 5 days, can put to use.
To get direct advice from APT Vietnam on KERASEAL ADO40, investors and contractors please contact us at 0904 339 299!